Время нагрева
Чем больше в стали углерода и специальных примесей, тем менее она теплопроводна и медленнее должен быть ее нагрев.
Поверхностные слои металла, нагретые до более высокой температуры, стремятся расшириться.
Этому расширению препятствуют внутренние, менее нагретые слои.
В результате поверхностные слои будут испытывать напряжения сжатия, а внутренние - напряжения растяжения.
Величина напряжений зависит от времени (скорости) нaгpeвa: чем больше скорость нагрева, тем больше разность температур между поверхностью и сердцевиной и, следовательно, тем выше напряжения.
Величина возникающих напряжений не должна превосходить допустимую, так как в металле могут образоваться трещины.
Наиболее опасно возникновение внутренних напряжений при нагреве до температур 500-600ºС, когда металл обладает малой пластичностью.
При более высоких температурах возникновение внутренних напряжений неопасно, так как металл становится пластичным.
При термической обработке (в печах) возможны три способа нaгpeвa:
- 1) детали загружают в холодную или разогретую до невысокой температуры печь: печь нагревают с деталями до заданной температуры, время нагрева большое, но разность температур по сечению небольшая - этот способ применяют при нaгpeвe деталей из высоколегированных сталей и сложной формы;
- 2) детали загружают в печь, имеющую постоянную заданную температуру: время нагрева меньше, чем при первом способе, но разность температур по сечению больше - этот способ нагрева применяют чаще;
- 3) детали загружают в печь, имеющей температуру выше заданной: по мере нагрева деталей температуру снижают до заданной, при этом способе нагрева, разность температур и возникающие внутренние напряжения наибольшие - этот способ форсированного нагрева.
Время нагрева зависит также от расположения деталей в печи и от их взаимного расположения.
Детали нагреваются быстрее при всестороннем подводе тепла; самый медленный нагрев – при расположении нескольких деталей вплотную (продолжительность нагрева увеличивается в 4 раза).
Все три приведенных способа применимы для определения времени нaгpeвa деталей диаметром (стороной квадрата) 3-100 мм.
Химическое действие нагревающей среды
При нaгpeвe деталей в печах металл взаимодействует с атмосферой печи.
Результатом такoгo взаимодействия является окисление, ведущее к образованию окалины на поверхности нaгpeaeмoгo металла, и обезуглероживание--частичное или полное выгорание углерода в поверхностных слоях стали.
Окисление приводит к потерям металла, усложняет обработку деталей, затрудняет получение высокой и равномерной твердости.
Потери металла при нaгpeвe составляют до 3% массы обрабатываемых деталей.
В обезуглероженном слое появляются «мягкие пятна» и возникают растягивающие напряжения, что снижает прочность, износостойкость и предел выносливости, т.е.снижает срок службы деталей.
В состав печной газовой атмосферы входят кислород, окись углерода, двуокись yглерода, водород, азот, метан, водяной пар.
Действие этих газов на сталь различно.
Водород обезуглероживает, окись углерода и метан науглероживают.
Водяной пар, двуокись углерода и кислород окисливают и обезуглероживают.
Процесс окисления.
Вначале происходит химическая реакция между металлом и окисляющим газом, в результате чего на поверхности металла образуется окисная пленка.
Дальнейший процесс окисления--это диффузия атомов кислорода сквозь пленку (к металлу) с окислением на границе металл--пленка; диффузия атомов металла сквозь пленку на ее наружную поверхность с окислением на границе пленка--газ или встречная диффузия атомов кислорода и металла.
На интенсивность окисления влияют состав и строение окисной пленки.
Если пленка пористая, окисление происходит интенсивно, если плотная--окисление замедляется или даже совершенно прекращается.
Процесс окисления есть диффузионный процесс; чем выше скорость диффузии, тем выше скорость окисления.
С повышением температуры нaгpeвa процесс диффузии резко ускоряется, поэтому и окисление будет происходить тем в большей степени, чем выше температура нагрева
В атмосфере влажного воздуха окисление происходит и при температуре 200°С; образующаяся окисная пленка состоит из окисла Fе2О3.
С повышением тeмпературы (выше 100°С) образуется плотный слой окислов Fе2О3 и Fе3О4.
При температуре выше 570°С кроме окислов Fе2О3 и Fе2О4 образуется менее плотный окисел FeO по следующм реакциям:
Fe + CО2↔FeO + СО;
Fe + Н2 О↔FeO + Н2;
2Fe + О2↔2FeO
(основная часть кислорода печной атмосферы находится в виде СО2 и Н2О).
С образованием окисла FeO окисление железа резко возрастает; при этом образуется слой окалины.
Поэтому практически детали предохраняют от окисления при нaгpeвe их до температур выше 500°С.
Параллельно с окислением протекает процесс обезуглероживания, т. е. взаимодействие газов печной атмосферы с углеродом.
Углерод может находиться в стали в виде карбида железа Fе3С или в твердом растворе [Feγ (С)].
Обезуглероживание скрытый дефект. Его можно обнаружить измерением твердости и по структуре стали.
Степень обезуглероживающеrо действия печной атмосферы зависит от содержания в стали углерода и легирующих элементов; например, хром уменьшает, а кремний, вольфрам, молибден, ванадий увеличивают склонность к обезуглероживанию.
На процесс обезуглероживания влияет и температура нaгpeвa; чем выше температура, тем интенсивнее протекает обезуглероживание.
Для сохранения постоянства химического состава поверхности деталей при данном режиме нaгpeвa и определенном химическом составе стали необходимо создать условия равновесия между металлом и печной атмосферой, т. е. иметь определенное соотношение окисляющих, обезуглероживающих, восстанавливающих и науглероживающих rазов.
Применение защитных атмосфер.
Для предохранения деталей от окисления и обезуглероживания при высоких температурах в рабочее пространство печи искусственно вводят защитную газовую среду, называемую защитной и контролируемой атмосферой.
Применяемая контролируемая атмосфера должна иметь низкую стоимость, быть простой в приготовлении, не должна образовывать излишних количеств сажи и кокса, не окислять и не обезуглероживать поверхность деталей при термической обработке.
Для защиты от окисления могут применяться инертные газы: аргон, неон и чистый азот, не содержащие даже следов кислорода, а также продукты диссоциации аммиака. Указанные газы требуют дополнительной очистки от агрессивных примесейи осушки, что повышает стоимость защитного газа в 2-3 раза.
В связи с этим чистые газы применяются для защитных атмосфер ограниченно.
В современном машиностроительном производстве применяют контролируемые атмосферы двух типов:
- 1) экзотермическую нейтральную при температуре ниже 700°С;
- 2) эндотермическую «универсальную», нейтральную при температуре выше 700°С (ниже 700°С она взрывоопасна).
Наиболее широкое применение находит эндотермическая атмосфера (эндогаз), которая применима как для безокислительного нaгpeвa, так и для цементации. Характерной особенностью эндотермической атмосферы является то, что результаты ее взаимодействия с нагретой сталью зависят только от содержания влаги, количество которой контролируется определением температуры точки росы.
Следовательно, по температуре точки росы контролируется содержание углерода на поверхности стальной детали (углеродный потенциал) в момент установления равновесия с атмосферой данного состава.
Применение расплавленных солей.
Предохранение деталей от окисления и обезуглероживания осуществляется также наrpeвoм в хорошо раскисленных расплавленных солях. Расплавленные соли или их смеси являются распространенными средами для нaгpeвa.
Широкое применение при термической обработке соляных ванн объясняется тем, что расплавленные соли по сравнению с другими нагревающими (газовыми, воздушными) и охлаждающими (вода, масло, воздух) средами обладают большими преимуществами.
Основные преимущества соляных ванн следующие:
- более быстрый и равномерный нaгpeв;
- более высокая производительность;
- меньший рост зерна при нaгpeвe;
- удобство местнoгo нагpeвa;
- уменьшение коробления стержневых деталей;
- возможность нaгpeвa деталей в вертикальном положении;
- меньшие внутренние напряжения и деформация;
- исключение возможности образования трещин (при охлаждении в расплавленных солях);
- предохранение от окисления и обезуглероживания при нaгpeвe и при переносе деталей из ванны в закалочный бак (детали покрыты тонкой пленкой соли).
В зависимости от интервала рабочих температур соляные ванны условно подразделяют на высоко-, cpeднe- и низкотемпературные.
Общим недостатком расплавов солей, как нагревающих сред, является их обезуглероживающее действие.
Во избежание обезуглероживания деталей при нaгpeвe в соляных ваннах необходимо периодически производить раскисление ванн.
Раскисление высокотемпературных соляных ванн (с хлористым барием) обычно производится молотым 75 %-ным ферросилицием, который добавляется в расплавленную соль 1-2 раза в смену в количестве 150-200г. за один прием, а также бурой.
Раскисление cpeднeтeмпературных соляных ванн производится: бурой через каждые 4ч работы добавляется 200-300г. буры; желтой кровяной солью в количестве 1-2% массы солей; древесным углем, для чего на дно ванны опускают на l0-15 мин ковш с отверстиями, наполненный уrлем.
Происходящее вначале бурление ванны с появлением значительного количества языков пламени постепенно уменьшается и затем прекращается, что и указывает на конец раскисления.
Раскисление низкотемпературных соляных ванн не производят.
Применение защитных покрытий.
Новое в безокислительной термической обработке применение защитных покрытий--стекловидных эмалей.
Для таких покрытий применяют механические смеси тонких порошков стекол с огнеупорными наполнителями
В процессе нaгpeвa происходит плавление легкоплавких, а затем тугоплавких составляющих смеси, и тем самым обеспечивается получение стекловидной расплавленной пленки, изолирующей металл от печной атмосферы.
Отжиг
Отжигом называют процесс термической обработки, заключающийся в нaгpeвe стали до определенной температуры и последующем, как правило, медленном охлаждении для получения более равновесной структуры.
Отжиг является предварительной операцией термической обработки, подготавливающей структуру стали к последующим технологическим операциям, например, к обработке заготовок на металлорежущих станках и окончательной термической обработке (закалке с отпуском) деталей.
Но отжиг используют и как окончательную термическую обработку в том случае, если получаемые в результате этой операции свойства удовлетворяют требованиям, предъявляемым к данной детали.
Полный отжиг характеризуется нaгревом стали на 20-30°С выше температуры интервала превращений, выдержкой при этой температуре и медленным охлаждением до температуры ниже интервала превращений.
При таком отжиге происходит полная фазовая перекристаллизация.
Данному виду отжига подвергают доэвтектоидную сталь с неравномерным или крупным зерном, а также с полосчатой структурой для создания мелкой зернистости, понижения твердости и повышения пластичности, снятия внутренних напряжений, улучшения обрабатываемости.
При полном отжиге доэвтектоидную сталь нагревают до температуры на 20-30°С выше температуры в точке Ас3, т. е. на 20-30°С выше линии GS диaгpaммы железо--цементит.
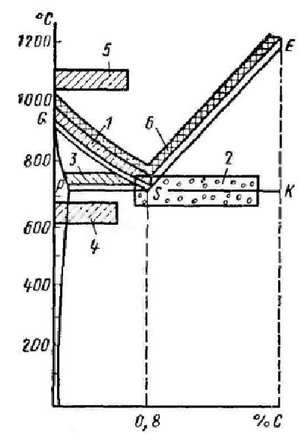
Рис.1. Температура нагрева стали для отжига и нормализации.
1-полный отжиr; 2-отжиг на зернистый перлит; 3-неполны отжиr; 4-рекристаллизационный отжиr; 5-диффузионныйотжнr; 6-нормализация
При нaгpeвe до такой температуры крупная исходная феррито-перлитная структура превращается в мелкую структуру аустенита.
При последующем медленном охлаждении для углеродистой стали со скоростью 120-150°С/ч до 450-550°С и далее на воздухе из мелкозернистого аустенита образуется мелкая феррито-перлитная структура.
При отжиге легированной стали скорость охлаждения должна быть порядка 30-70°С/ч, это связано с тем, что легирующие элементы повышают устойчивость аустенита.
Для сокращения продолжительности отжига легированные стали целесообразно подвергать изотермическому отжигу.
Заэвтектоидную сталь полному отжигу не подверrают.
Для полного отжига заэвтектоидную сталь нужно нaгpeвaть до температуры на 20-30°С выше точки Аст, т.е. на 20-30°С выше линии SE диаграммы железо--цемеитит.
При нaгpeвe до такой температуры будет происходить превращение исходной структуры цементит и перлит в структуру аустенита.
При последующем медленном охлаждении цементит будет выделяться по границам зерен аустенита и после превращения аустенита в перлит при температурах нeмнoгo ниже температуры в критической точке Ar1, в результате образуется структура цементит и перлит, но цементит будет расположен в виде сетки по границам зерен перлита.
Сталь с такой структурой имеет низкую вязкость, неравномерное распределение твердости по сечению, плохо обрабатывается на станках.
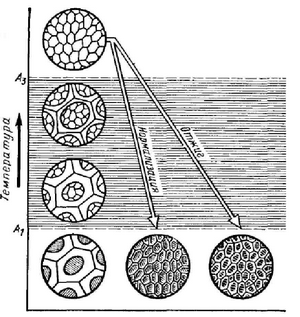
Рис.2. Схема изменения структуры доэвтектоидной стали при отжиrе и нормализации
Неполный отжиг характеризуется нaгpeвoм стали до одной из температур в интервале превращений (выше точкиАС1, но ниже точки Ас3), выдержкой и медленным охлаждением.
При таком отжиге происходит перекристаллизация только перлита, а избыточная фаза (в доэвтектоидных сталях-феррит) остается без изменения.
Изотермический отжиг заключается в нaгpeвe до температуры выше температуры в точке Ас3 для доэвтектоидной и АС1 для заэвтектоидной стали, выдержке, ускоренном охлаждении до температуры нeмнoгo ниже температуры в точке Ar1, изотермической выдержке при этой температуре для завершения перлитноrо превращения и охлаждения на воздухе.
Таким образом, характерной особенностью изотермического отжига является образование феррито-цементитной смеси из аустенита при постоянной температуре, а не при непрерывном охлаждении, как при полном отжиге.
Отжиг на зернистый перлит (зернистый цементит) заключается в нaгpeвe стали до температуры несколько выше температуры в точке Ас1, выдержке и последующем охлаждении для сфероидизации цементита и получения зернистого перлита.
Этому виду отжига подвергают детали из заэвтектоидной и эвтектоидной сталей.
Детали из стали со структурой зернистого перлита обладают по сравнению с деталями из стали со структурой пластинчатого перлита большей пластичностью, равномерным распределением твердости по сечению и лучшей обрабатываемостью на станках.
Диффузионный отжиг (гомогенизация) характеризуется нaгpeвом стали до температуры значительно выше температуры интервала превращений (на 180-300°С) с последующим медленным охлаждением.
Такой отжиг применяют для выравнивания химической неоднородности (путем диффузии) зерен твердого раствора, т. е. уменьшения микроликвации в фасонных стальных отливках и в слитках главным образом легированной стали.
Рекристаллизационный отжиг используют для стальных деталей, деформированных в холодном состоянии.
Холодная деформация (прокатка, волочение и т.п.) влияет на строение и механические свойства стали.
В результате холодной деформации, например низкоуглеродистой стали, зерна стали (феррита) вытягиваются в направлении деформации. При сильной деформации зерна не только вытягиваются, но и дробятся.
В стали деформации подвергается пластичный феррит, а цементит, обладающий высокой твердостью, почти не деформируется и оказывает сопротивление деформации.
В связи с этим, чем больше углерода, тем труднее сталь поддается деформации.
Сталь с зернистым цементитом легче деформируется, чем сталь, имеющая структуру пластинчатого перлита.
В результате холодной деформации повышаются твердость и прочность и понижается пластичность стали.
Изменение механических свойств стали под влиянием холодной деформации называется наклепом или нагартовкой.
Деформацией в холодном состоянии изготовляют, например, проволоку (волочением), листы, ленты (прокаткой).
Возникающий в процессе деформации наклеп стали может достигнуть такой величины, что сталь становится хрупкой и дальнейшая деформация ее становится невозможной.
Для возвращения стали пластичности и возможности дальнейшей ее деформации проводится рекристаллизационный отжиг.
Нормализация
Нормализацией называют процесс термической обработки, заключающийся в нагреве до температуры на 40-50°С выше температуры в точке Ас 3 для доэвтектоидной или в точке Асm для заэвтектоидной стали с последующим охлаждением на воздухе для получения тонкопластинчатой перлитной структуры.
При нормализации низкоуглеродистых сталей происходят те же процессы, что и при отжиге, т.е. измельчение зерен.
Но, кроме того, вследствие охлаждения более быстрого, чем при отжиге, и получающегося при этом большего переохлаждения перлит получается более дисперсным, а его количество большим, так как частично подавляется выделение феррита или цементита и образуется квазиэвтектоид.
Механические свойства при этом оказываются более высокими (повышенная прочность и твердость), чем при более медленном охлаждении (при отжиге).
Нормализация по сравнению с отжигом - более экономичная операция, так как не требует охлаждения вместе с печью.
Для низкоуглеродистых сталей нормализация широко применяется вместо отжига.
Но для высокоуглеродистых сталей нормализация не может заменить отжиr, так как твердость таких сталей после нормализации получается значительно более высокой, чем после отжига (например, твердость стали У10 после отжиrа НВ≤197, а после нормализации НВ 255-320).
Нормализацию применяют также для устранения цементитной сетки в заэвтектоидных сталях.
При нaгpeвe заэвтектоидной стали с цементитной сеткой выше температуры в критической точке Аст образуется структура аустенита.
Закалка
Выбор температуры.
Закалкой называется процесс термической обработки, заключающийся в нaгpeвe стали до температуры выше критической и последующем достаточно быстром охлаждении для получения вместо механической смеси фаз пересыщенного твердoгo раствора с искаженной решеткой (мартенсита).
В результате закалки прочность и твердость стали повышаются, а пластичность снижается.
Температуру нагрева при закалке углеродистых сталей выбирают по левой нижней части диаграммы железо--цементит.
При закалке доэвтектоидные стали нагревают до температуры на 30-50°С выше температуры и верхней критической точке Ас3, т.е. выше линии GS диаграммы железо--цементит.
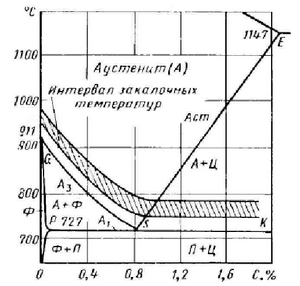
Рис.3. Оптимальный интервал температур закалки для углеродистой стали
При таком нагреве исходная феррито-перлитная структура превращается в аустенит, а после охлаждения со скоростью больше критической образуется структура мартенсита.
При нагреве доэвтектоидной стали до более низкой температуры, например выше критической точки Ас 1, т.е. выше линии PS диаграммы железо--цементит, но ниже точки Ас 3 структура и свойства стали будут изменяться следующим образом: исходная феррито-перлитная структура при таком нагреве не будет полностью превращаться в аустенит, а часть феррита останется не превращенным и структура будет аустенит и феррит.
Феррита в стали останется тем больше, чем температура нагрева ближе к температуре в точке Ас 1.
Структура после охлаждения будет мартенсит и феррит.
Феррит, имеющий низкую твердость, понижает общую твердость закаленной стали; такая закалка называется неполной.
При закалке заэвтектоидные стали нагревают до температуры на 30-50°С выше температуры в нижней критической точке, т.е. выше линии SK диаграммы железо--цементит.
Так как эта линия горизонтальная и соответствует температуре 727°С, для заэвтектоидной стали можно указать интервал температуры нагрева для закалки 760-790°С.
При таком нагреве исходная структура перлит и цементит не будет полностью превращаться в аустенит, а часть вторичного цементита останется нерастворенной и структура будет аустенит и цементит.
После охлаждения со скоростью больше критической аустенит превратится в мартенсит.
Структура заэвтектоидной стали будет состоять из мартенсита и цементита; такая закалка будет неполной.
Но если неполная закалка доэвтектоидных сталей ухудшает их свойства, то неполная закалка заэвтектоидных сталей улучшает их свойства и является
нормальной.
Это объясняется тем, что в заэвтектоидных сталях в результате неполной закалки сохраняется избыточный цементит, обладающий большей твердостью по сравнению с мартенситом.
Охлаждающие среды.
Скорость охлаждения стали, нагретой до температуры закалки, влияет на результат закалки.
Оптимальной закалочной средой является та среда, которая быстро охлаждает деталь в интервале температур минимальной устойчивости аустенита (550-650°С), чтобы предупредить его распад на феррито-цементитную смесь, и замедленно (или с очень большой скоростью) - в интервале температур мартенситноrо превращения (ниже 200-300°С), чтобы обеспечить одновременность мартенситообразования во всех зонах охлаждаемой детали и этим снизить опасность образования трещин.
Наиболее распространенными закалочными средами являются вода, водные растворы солей, щелочей, масло, расплавленные соли.
При охлаждении в воде и масле, температура кипения которых ниже температуры охлаждаемых в них деталей, скорость охлаждения различна в начальном, среднем и конечном периодах охлаждения и подразделяется на три стадии:
- 1. пленочноrо кипения;
- 2. пузырчатоrо кипения;
- 3. конвективнoro теплообмена.
Между этими стадиями в промежутках наблюдается переходное состояние.
Стадия пленочного кипения характеризуется образованием вокруг охлаждаемой детали паровой пленки, отделяющей раскаленную поверхность от жидкости, и поэтому скорость охлаждения на данной стадии сравнительно невелика.
Стадия пузырчатого кипения наступает при более низких температурах охлаждаемой поверхности, когда паровая пленка разрушается, создается непосредственный контакт жидкости с деталью; при кипении жидкости возникают пузырьки пара, на что затрачивается большое количество тепла, в связи с чем охлаждение происходит с большой скоростью.
Стадия конвективного теплообмена наступает при понижении температуры на поверхности ниже температуры кипения жидкости.
Скорость теплоотвода в этой стадии низка, и охлаждение протекает с небольшой скоростью.
Вода охлаждает быстрее, чем масло (в 6 раз при 550-650°С и в 28 раз при 200°С).
Поэтому воду применяют для охлаждения деталей из сталей с большой критической скоростью закалки (углеродистые стали), а в масле охлаждают детали из стали с малой критической скоростью закалки (легированные стали).
Недостатком воды является большая скорость охлаждения при пониженных температурах, что вызывает неодновременность образования мартенсита в разных зонах охлаждаемой детали, приводит к появлению больших структурных напряжений и создает опасность возникновения трещин.
При нагреве воды ее закаливающая способность снижается в области высоких температур (550-650°С), а скорость охлаждения в области температур мартенситного превращения остается высокой.
Поэтому охлаждение в горячей воде не уменьшает возможности образования трещин.
Добавление к воде солей и щелочей (8-12%-ныe водные растворы NaCl и NaOH) значительно увеличивает ее закаливающую способность в связи с расширением интервала пузырчатого кипения (почти полностью исключается стадия пленочного кипения).
Для охлаждения применяют также водо-воздушные смеси, подаваемые через форсунки.
Изменением соотношения воды и воздуха, а также давления смеси можно менять скорость охлаждения.
Масло обладает небольшой скоростью охлаждения в области температур мартенситного превращения, что обеспечивает одновременность мартенситообразования, и поэтому опасность образования трещин резко уменьшается.
Кроме того, закаливающая способность не изменяется с повышением температуры масла до 150°С.
В качестве охлаждающей среды при закалке используют также «кипящий» (псевдоожиженный) слой.
Псевдоожижение заключается в интенсивном перемешивании частиц твердого зернистого материала (например, корунда, песка, руды, металлического порошка) восходящим потоком газа.
Прокаливаемость стали.
Под прокаливаемостью подразумевают способность стали закаливаться на определенную глубину.
Прокаливаемость не надо смешивать с закаливаемостью, которая характеризуется максимальным значением твердости, приобретенной сталью в результате закалки. Прокаливаемость одна из важнейших характеристик качества стали, во многом определяющая служебные свойства, надежность и долговечность работы машин.
Знать фактическую прокаливаемость различных сталей необходимо для их рационального применения.
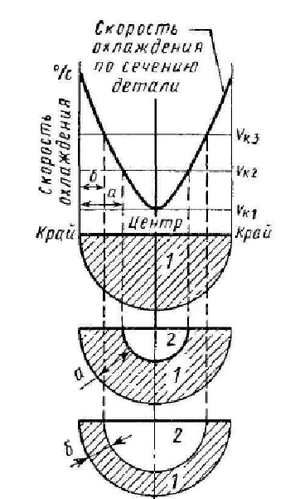
Рис.4. Зависимость прокаливаемости от критической скорости закалки
1-мартенсит (полная прокаливаемость); 2-троостит, сорбит, перлит
Прокаливаемость стали зависит от критической скорости Vк закалки.
Деталь прокалится насквозь, и мартенситная структура по всему сечению будет в том случае, если скорость охлаждения в сердцевине будет равна (или больше) критической скорости Vк 1 закалки данной стали.
Если в тех же условиях охлаждения закаливают такие же детали, но из стали с более высокими значениями критической скорости (VK2 , Vк3 ), то скорость охлаждения в сердцевине будет меньше критической скорости закалки для данной стали, и детали будут прокаливаться только на некоторую глубину, т.е. прокаливаемость будет неполной и в сердцевине образуются троостит, сорбит или сохранится исходная структура.
Следовательно, чем меньше критическая скорость закалки, тем больше прокаливаемость.
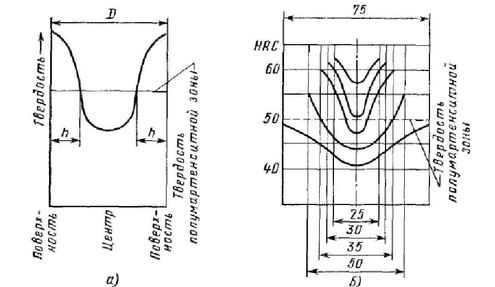
Рис.5. Распределение твердости по сечению
а-закаленного образца; б-закаленных цилиндрических образцов
D-диаметр образца; h-толщина закаленной зоны
Критическая скорость закалки уменьшается, и, следовательно, прокаливаемость увеличивается:
1) с повышением в стали содержания углерода и легирующих элементов (марганца, хрома, никеля, молибдена и других, за исключением кобальта), pаcтвoренных в аустените, повышающих устойчивость переохлажденного аустенита;
2) с укрупнением зерна аустенита (с уменьшением суммарной протяженности границ зерен аустенита, по которым преимущественно образуются центры кристаллизации).
Критическая скорость закалки увеличивается, и, следовательно, прокаливаемость уменьшается:
1) при неоднородной структуре, например при наличии карбидов, неметаллических включений, являющихся дополнительными центрами кристаллизации;
2) с уменьшением размера зерна аустенита (с увеличением суммарной протяженности границ зерен аустенита, по которым преимущественно образуются центры кристаллизации).
Прокаливаемость можно определить по излому, измерением твердости по сечению образца и измерением твердости по длине образца (методом торцовой закалки).
Наиболее распространенным методом определения прокаливаемости в связи с его простотой и универсальностью является метод торцовой закалки, впервые предложенный акад. Н. Т. Гудцовым.
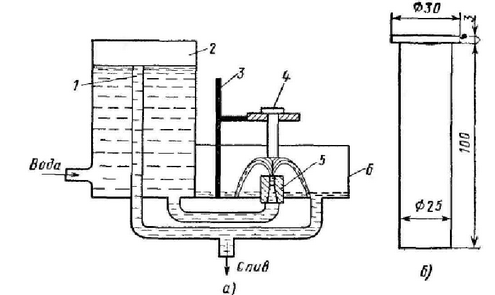
Рис.6. Установка и образец для торцовой закалки
1-уравнительная трубка для создания постоянства напора; 2-напорный бачок; 8-штатив; 4-образец; 5-сопло; 6-сливная коробка
Цилиндрический образец (диаметром 25мм и длиной 100мм) нагревают (с защитой от окисления) до температуры закалки и после выдержки помещают в специальную установку, в которой образец охлаждается с торца струей воды.
Для измерения твердости закаленного образца по всей его длине с двух противоположных сторон ошлифовывают две фаски.
Твердость измеряют от охлажденного торца.
Внутренние напряжения в закаленной стали.
При закалке в детали возникают значительные внутренние напряжения - термические и структурные.
Термические напряжения возникают от нepaвнoмepнoгo охлаждения поверхности и сердцевины детали.
Сердцевина охлаждается медленнее поверхности, и разность температур ∆T тем больше, чем ниже температура поверхности.
Период охлаждения, когда разность температур достигает максимума, является наиболее вероятным для развития внутренних напряжений.
В этот период охлаждения в поверхностных слоях детали будут возникать напряжения растяжения, а в сердцевине - напряжения сжатия.
Структурные напряжения возникают в результате тoro, что превращение аустенита в мартенсит (связанное с увеличением объема) в разных местах детали происходит не одновременно.
Температура мартенситного превращения сначала достигается в поверхностных слоях, в которых появляются временные сжимающие напряжения, а во внутренних слоях напряжения растяжения.
Затем мартенситное превращение протекает во внутренних слоях и знак напряжений на поверхности и в сердцевине изменяется.
Способы закалки.
Непрерывную закалку в одной среде применяют наиболее широко.
Деталь нагревают до температуры закалки и охлаждают в одной среде.
Если охлаждение производят в жидкой среде (воде, масле), то для paвномернoгo охлаждения деталь, погрузив в жидкую среду, перемещают в вертикальной плоскости или круговыми движениями.
Для равномернoгo охлаждения жидкость перемещают с помощью лопастей, установленных в закалочном баке, или непрерывно подают и отводят из закалочного бака охлаждающую жидкость.
Если требуется закалить не всю деталь, а только определенную часть, в охлаждающую жидкость погружают эту часть детали или применяют струйное охлаждение.
Такую закалку называют местной.
Для равномерной закалки и уменьшения коробления (особенно длинных цилиндрических деталей, тонких плоских деталей и др.) применяют специальные закалочные машины и прессы.
В закалочной машине или закалочном прессе деталь при охлаждении находится в зажатом положении (например, валы и оси между зажимными роликами, зубчатые колеса - в штампах, пилы - между плитами и т. п.).
При закалке в двух средах (прерывистая закалка,) деталь охлаждают до 300-400°С в энергично действующем охладителе - воде, а затем для окончательного охлаждения переносят в слабый охладитель - масло.
Такая закалка иначе называется закалкой в воде с переброской в масло.
Ступенчатая закалка заключается в том, что нагретую до температуры закалки деталь охлаждают в солях, имеющих температуру немного более высокую, чем
температура начала мартенситного превращения для данной стали.
После выдержки при данной температуре в течение времени, необходимого для выравнивания температуры по всему сечению, деталь вынимают из соляной ванны и охлаждают на воздухе.
Для деталей из легированных сталей ступенчатую закалку применять нецелесообразно, так как они закаливаются в масле, которое достаточно медленно охлаждает в интервале температур мартенситного превращения.
Изотермическую закалку, впервые предложенную Д.К.Черновым, применяют широко.
Так же, как и при ступенчатой закалке, охлаждение деталей, нагретых до температуры закалки, производится в соляных ваннах.
Температура соляной ванны при изотермической закалке 250-400°С.
Детали выдерживают в соляной ванне в течение времени необходимого для полного распада аустенита.
Для нагрева деталей при закалке применяют камерные, конвейерные печи и другие.
Большое распространение имеют тигельные электрические и электродные печи-ванны.
Печи-ванны удобны в работе; нагрев деталей в них происходит быстрее, чем в камерных печах.
При нагреве в печах-ваннах детали находятся в расплавленной соли; в них также удобно нагревать детали путем частичнoгo погружения в расплавленную соль.
Отпуск
Отпуском называется процесс термической обработки, заключающийся в нагреве закаленной стали до температуры не выше температуры в точке Ас 1, обусловливающей частичный или полный распад мартенсита, выдержке при заданной температуре и охлаждении обычно на воздухе (сталь, склонную к отпускной хрупкости, охлаждают в воде).
Отпуск является окончательной операцией термической обработки и проводится для повышения пластичности, снижения или почти полного устранения внутренних напряжений, уменьшения хрупкости закаленной стали, стабилизации структуры и размеров закаленных деталей.
Низкий отпуск заключается в нагреве стали до температуры ниже 250°С и охлаждении для получения мартенсита отпуска и частичного снятия внутренних напряжений.
В результате низкого отпуска сталь становится менее хрупкой, твердость и износостойкость сохраняются высокими.
Средний отпуск заключается в нагреве стали до температуры 350-500°С и охлаждении для получения структуры троостита отпуска.
В результате среднего отпуска твердость закаленной стали снижается до HRC 40-50, тогда как предел упругости, имеющий после закалки стали наименьшее значение, достигает максимальной величины.
Поэтому среднему отпуску подвергают пружины, рессоры и другие упругие элементы.
Высокий отпуск заключается в нагреве стали до температуры 500-б80°С и охлаждении для получения структуры сорбита отпуска.
В результате высокoгo отпуска твердость закаленной стали снижается до НВ 250-350, прочность снижается в 1,5-2 раза, в несколько раз увеличиваются пластичность и вязкость и почти полностью снимаются внутренние напряжения.
Низкий отпуск часто проводят в масляных ваннах.
Для высокoгo отпуска используют электропечи; для pавномернoгo нагрева применяют электропечи (шахтного типа) с циркуляцией нагретого воздуха с помощью вентилятора.
Кроме обычного отпуска используют также самоотпуск, при котором нагретая под закалку деталь охлаждается не полностью, чтобы остаточное, сохранившееся в детали тепло произвело отпуск.
Такое совмещение в одну операцию закалки и отпуска называют закалкой с самоотпуском.
В современных термических цехах мaccoвoгo производства для термической обработки применяют aгpeгаты непрерывного действия, состоящие из различнoгo оборудования, в котором непрерывно осуществляются все виды термической обработки данной детали.
Дефекты, возникающие при термической обработке
- Недогрев получается в том случае, если сталь была нагрета до температуры ниже критической.
- Перегрев получается в том случае, если сталь была нагрета до температуры намного выше критической или при оптимальной температуре была дана очень большая выдержка. При перегреве происходит рост зерна аустенита, а после закалки образуется крупноигольчатый мартенсит.
- Пережог получается в том случае, если сталь была нагрета до температуры, близкой к температуре начала плавления.
- Закалочные трещины являются результатом резкого охлаждения или нагрева вследствие возникающих при этом внутренних напряжений как термических, так и структурных; перегрева; нepaвнoмepнoгo охлаждения; наличия в деталях острых углов, глубоких рисок и т.п., в которых при закалке из-за концентрации внутренних напряжений создаются условия для образования трещин.
Структурные изменения, происходящие в металле при термической обработке, вызывают изменение объема (деформацию), а неравномерность охлаждения - искажение внешней формы (коробление).
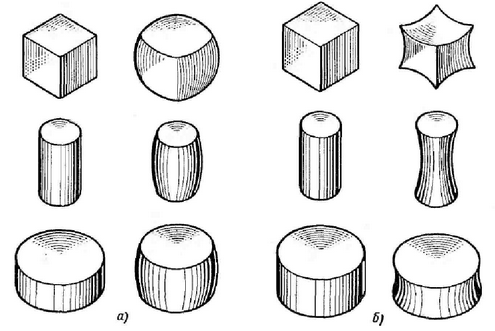
Рис.7. Тела простой формы после деформации под влиянием тепловых и структурных напряжений
Для предотвращения деформаций и коробления необходимо обеспечить медленное охлаждение в интервале мартенситного превращения путем ступенчатой и изотермической закалок, закалки в двух средах, изготовления деталей из легированных сталей, чтобы их можно было закаливать в масле.
Уменьшение коробления достигается также правильным способом погружения детали в охлаждающую жидкость, например, длинные стержневые детали необходимо охлаждать в вертикальном положении, закаливать в закалочных машинах и штампах и др., коробление детали исправляют правкой или рихтовкой.
|